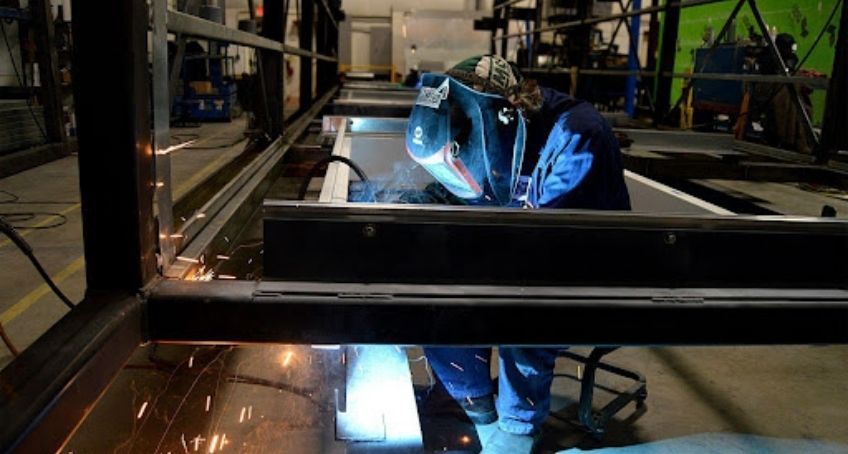
Soplo de Arco Magnético en soldadura: Qué es y cómo reducirlo
Soplo de Arco Magnético en soldadura: Qué es y cómo reducirlo
Son muchas las consideraciones y conocimientos que hay que tener en cuenta a la hora de realizar trabajos de soldadura por su exigencia y complejidad. El soplo magnético puede ser una de las dificultades con la que nos encontramos cuando soldamos con arco de corriente continua.
El soplo de arco magnético dificulta mucho la soldadura, reduce la velocidad de avance y disminuye la calidad de esta. Además, puede causar salpicaduras excesivas, porosidad y demás problemas que entorpecen nuestros trabajos de soldadura. Pero ¿qué es exactamente y cómo podemos prevenirlo?
Aquí os explicamos algunas maneras de evitar los soplos de arco magnéticos. Sin embargo, la principal manera de prevenirlo es acudir a una empresa especializada en máquinas de soldadura para adquirir el equipo de soldadura adecuado
El Soplo de Arco Magnético: ¿Qué es?
El soplo magnético es un efecto que se produce por la acción que tiene un campo magnético sobre una corriente eléctrica. Este fenómeno se produce en la soldadura de corriente continua debido a fuerzas electromagnéticas produciendo una desviación en el arco, el cual cambia de dirección haciendo movimientos violentos.
El soplo magnético es causado por el arco, cuando no va por el camino más corto del electrodo a la pieza, sino por otros campos electromagnéticos que aparecen debido a la intensa corriente necesaria para soldar.
Los casos más comunes en los que se produce estos soplos son, al soldar cerca de los extremos de una pieza, cuando soldamos cerca de la conexión de masa y si estamos soldando cerca de grandes piezas ferromagnéticas.
¿Cómo lo reducimos?
No todos los soplos de arco son perjudiciales. De hecho, una pequeña cantidad puede, algunas veces, ser usado beneficiosamente. Existen varios métodos para reducir los efectos del soplo magnético:
Haz un cambio a corriente alterna: se neutralizan los efectos magnéticos debido al continuo y rápido cambio de dirección de la corriente.
Reduce la corriente de soldadura: al reducir la intensa corriente, se evita la creación de campos electromagnéticos causantes del soplo.
Inclina el electrodo contra la pieza en la dirección del soplo de arco
Utilizar la técnica de soldadura de retroceso (paso atrás)
Enrolla el cable de la masa alrededor de la pieza: de esta manera la corriente de retorno pasará a través del equipo en una dirección de manera que el campo magnético predeterminado neutralice el campo magnético causante del soplo.
Esperamos que estas recomendaciones puedan haber sido de ayuda para futuros trabajos de soldadura con arcos de corriente continua. Si sigues teniendo dudas, o quieres más información sobre algún producto puedes contactar con nosotros.